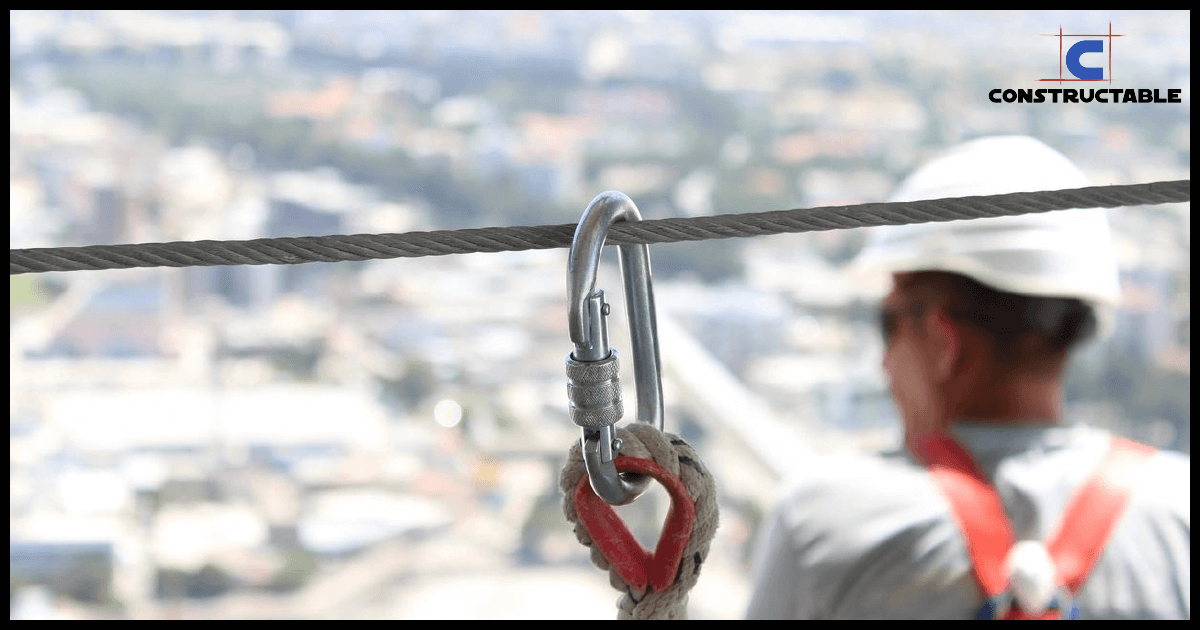
Design For Safety
The drive toward safety is a common mantra in the construction industry, fueled by poor working conditions, horrific accidents, and mistakes of the past. But too often the refrain of “Safety is job #1” on a t-shirt and broadly-reaching employee campaign is a tired fantasy when it comes to a real job site. How can you get your team, your subcontractors, and your site visitors to buy into safety so that it truly becomes a part of your process, who you are as a company? We are talking about a wholesale, fully engaged safety program that welcomes new employees to join and perpetuates itself across all your future projects. That is the kind of safety that moves a company forward and protects its interests. The stakes are so high: people’s lives, your customers choosing to work with you or not, your “bondable-ness”, and your chance to win jobs. It is clear that if we fail on this one, we fail at everything. So just how do you infuse your company with safety?
How is it that we take painstaking steps with billions of dollars spent on design of our projects but neglect to design for safety? If you want a culture of safety then you must “design for safety” in construction.
1. Plan ahead.
“If you aim at nothing, you’re sure to hit it every time.” —Zig Ziglar
The principle rings true for work, construction, life in general, and particularly, safety. Without a design in mind for safety, your policies, procedures, and even sites will become a mishmash of safety behaviors, never rising to become the unified culture that successfully overcomes challenges and threats to the people on site. One worker will wear the proper PPE, but not practice safe backup and spotting techniques with vehicles and equipment. Another amateur will climb aboard the equipment to move it out of the way, but neglect to realize he is endangering everyone around him by not having the correct training. A pipefitter might wear eye protection and gloves but fail to realize that the framers above him just might drop hardware from heights onto his hard-hat-less head without even realizing they are there. Safety matters and you must design into it for it to matter to everyone else.
Practically deployed, planning ahead means setting advance time on your calendar for safety, safety inspections, and safety training.
Planning ahead means proactively acting on your site so that you do not react to its conditions. Is that pile of scrap wood really necessary? Are all nails and screws facing down? Have you considered parking conditions? Does your site have a safety plan? How often do you do toolbox talks? Do you require JSAs from your team?
Every single successfully-planned step protects you from lawsuit and pays dividends in happy workers, zero-accident sites, litigation-free projects, and a company/division/crew that can continue indefinitely. That is where the real win is, isn’t it? Every person goes home at night; your company continues another day; your customer is satisfied, even impressed; and employee job satisfaction can grow since you have taken care of their most basic need.
Failing to plan will destroy your reputation, culture, employee morale, and simply lose you jobs and money.
But what happens when not everyone sees it that way? And what is a leader who cares about safety to do?
2. Set the example.
“Be the change you wish to see in the world.” —Arleen Lorrance
If leadership does not care for safety, how would can we ever expect anyone else to care?
Leadership has distinct advantages for designing for safety:
A. They see the whole picture (i.e., lawsuits, EMR ratings, TRIR levels).
B. They have resources to invest (i.e., setting budgets, allocating funds, hiring personnel)
C. They are most visible.
While leaders have to care about safety and set the example, it is not enough for only the front office to set the example. Every single team member in a position of authority must do the same. If the superintendent does not wear a hard hat, who on the site will? If we do not care about safety, why should anyone else care?
3. Expend resources.
“Where your treasure is, there is your heart.” —Jesus Christ
Put your money where your mouth is. If your company sees you investing in safety, it is the foundation to a culture of doing the same.
We prioritize where our money is placed. The Great Teacher, 2,000 years ago said, “Where your treasure is, there is your heart.” I think he meant that what you invest in will drive your desires. It’s not the other way around. That brings good news: you can actually change what you think and what you want by simply investing in different things.
Too many companies have not invested in safety. Read that again: too many companies have not invested in safety.
Everyone around you will understand how important safety is when you put money into it, invest in training for your team, and divert resources to the right place.
But do not only put money into safety, put your time as an investment in your company, employees, and subcontractors. When the top of the team puts time—something you will never get back—into safety, those underneath you follow suit.
How inspiring is it for the on-the-site workers who are experiencing the need for safety every day to see the top brass modeling the time and training it takes to have a world-class safety program?
If you looked at your ledger and your calendar, how much of your heart have you put into safety? If the answer is “Not much”, then it is time to start spending on what is the most important investment in your company.
4. Design a culture of safety through the whole team.
“Inspect what you expect.”
Design for safety takes all of us. That is because all of us are affected by safety issues; all of us benefit from safe practices; and every single team can advance together in safety.
1. Design for safety starts at the top.
2. Design for safety is enforced in the middle.
3. Design for safety hits home when all employees prioritize it.
The whole idea about putting your money and time into safety is the very foundation of demonstrating that safety starts at the top. The CEO will likely never swing a hammer anymore. But she can invest in safety and set the tone for everyone else. The bean counters behind their desks will never wield a jackhammer, but they can support the process.
The middle of the company is the key to enforcing safety. One famous and oft-repeated saying, “Inspect what you expect” rings absolutely true here. Who will actually comply to safety standards if not followed up with? What the team does in the field is largely disconnected from glorious and ambitious safety programs hatched in the board room unless you have someone to make sure there is follow through, real, accountable, actionable follow through. That is where the middle management, the superintendents come in. If they do not care for safety, who will care for safety? If they do not enforce safety procedures, who will follow them?
The middle management can be a buffer between both sides of the company. They can enforce safety programs and roll it out to the team in a way that will be accepted. Additionally, reprimands from them while the team stumbles over themselves to follow guidelines do not go over as harshly as with upper management who could shutter an entire job site. To be clear, every person should be fired over safety offenses. But the superintendent has the chance to build relationships beforehand that cause team members to want to comply, so they won’t have to be fired later on. That is the power of enforcing from the middle. They are also grizzled, hardened veterans of the field who can demand and command respect from the team where a suit-wearing businessperson would only find mocking and contempt.
Lastly, you will never actually have a culture of safety—the end product of your design for safety initiatives—unless the boots on the ground adopt it. Safety hits home when all employees prioritize it. Whether it is some macho, “I’m tougher than a hard hat” kind of thinking or something else, every single team member has to prioritize safety. The proudest moment in an HSE manager’s life is to see even the front-line boots on the ground taking up the cause of safety.
The job is never done until everyone prioritizes safety every day on every site. That seems like a lofty, impossible goal, but it is a worthwhile one to set and invest in and strive toward. Set it and put proactive, measurable, attainable steps to get there.
Can we really build a better project and world by designing for safety in this way? Of course. And it is doable with the help of the entire team.
One final tip on safety:
5. Design for safety means demonstrating “What’s in it for me?”
“What’s in it for me?”
People really do not do anything they do not want to do.
They always ask, “What’s in it for me?”
But you—as a construction leader, HSE professional, superintendent, foreman, etc.—can you answer this question?
Under pain of being fired, getting dumped, losing out on an opportunity, missing out on an experience, for these things a person will comply to something he or she does not want to. But this is a compliance that will only go so far. And what happens when the threats run out? What happens when you can no longer intimidate someone into wearing a hard hat? At that point the relationship is over: either you fire the person, company, subcontractor or he or she knows that compliance is no longer required because your bluff has now been called.
Safety has to come from a place of understanding the benefits for me personally, not just to save the company from litigation or just to follow the rules. It is someone taking safety guidelines to heart rather than just a blind, angry compliance to what the boss says.
Yes, someone who wears a hard had because he or she has to is better to have than no hard hat at all, but that is not the ideal. And—just so you know—he or she takes off that hard hat when the superintendent is not looking. But a safety program that is designed to demonstrate the benefit to the individual himself or herself is one that will gain more acceptance for the fact that you proved to your team just why safety is important to them. It is the only way safety will stick with your employees and subcontractors.
Conclusion: Design for safety by planning ahead, setting the example, expending resources, and infusing it through the top, middle, and bottom, and demonstrating the “what’s in it for me” method.
Here at Constructable safety is a part of who we are; it’s in our DNA, daily practice, and every project. We will make your project correct with everyone on it safely following highest standards.
Start an estimate HERE or by writing estimating@constructable.pro. With safety prioritized and your project our privilege, your ideas will quickly become a reality.